The Cyber-Physical Production Systems
Sep 27, 2023 11:21:34 AM - 9 min read
Nicola La Palombara
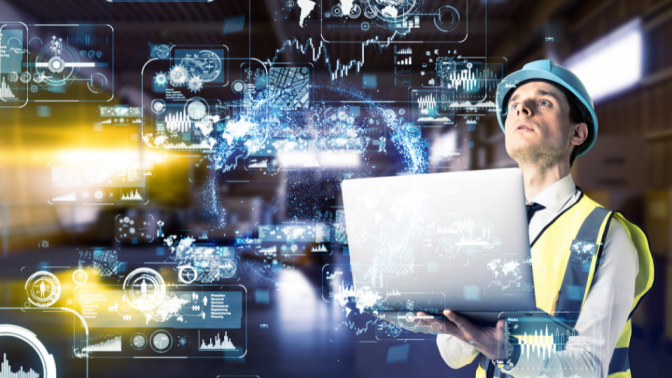
Driven by the requirements for highly customized products, increasing production systems complexity or shorter product life cycles, the fourth industrial revolution refers to the adoption of innovative technologies to drive the digitization and integration of value chain activities.
One of the main Industry 4.0 challenges is the introduction of decentralized architectures, which allow collaboration among autonomous entities to obtain higher production performances.
In this article, we will analyze the keystones of this revolution and what are the potential impacts on operational planning.
Cyber-Physical Systems as a confluence of the virtual and physical world
The new paradigm, that seems to encapsulate all the Industry 4.0 features, is known as cyber-physical system (CPS) and it is based on the idea of involving intelligent objects (agents) such as machines, parts, and products to obtain real-time data (control), evaluate them (computation) and communicate the results (communication) [1]. CPS represents a deep fusion of physical (sensors and actuators) and cybernetic (computer systems) components with constant network connection, autonomous control, and behaviour that adapts to the evolution of the environment. CPS extracts large amounts of data from physical processes and creates a virtual copy of the physical world, which commonly is identified as a digital twin.
The digital representation allows the physical resources and activities to be dynamically and realistically mapped in the virtual space for further data processing, simulation, and machine interconnections to be able to make decentralized decisions based on real-time system conditions.
In this way, the CPSs present an effective approach to developing and conducting an optimal planning strategy based on the results of digital twin simulations.
Cyber-Physical Systems in production planning and control systems
Among the wide possible utilizations, CPSs application in the field of production management gave rise to the term of Cyber-Physical Production Systems (CPPS). We can define CPPSs as systems of systems with a certain autonomy, which cooperate to carry out decision-making on all levels of production activities, allowing them to respond to unforeseen events and evolve over time. These systems use communication interfaces both to exploit CPSs' cooperation with each other and to enable a deep collaboration with humans, with the final goal to achieve intelligent, resilient, and self-adaptive systems [2].
Fig. 1 proposes an integrated synthesis of these characterizations, highlighting intelligence, connectivity, and responsiveness as the three main characteristics of CPPSs.
The key capabilities emphasized by this architecture are:
- Self-sensing: they continuously capture, exploit, and share information from and to the environment
- Self-deciding: they can take data-driven decisions based on real-time conditions of the system.
- Self-adapting: the reactivity to face unexpected events thanks to the faster transmission of information through the entire system.
Expectations vs implementation
The 5C architecture [3] details the step-by-step implementation of CPS for manufacturing applications:
- Smart Connection: integration of all elements in the physical space to collect data
- Data Conversion: tools and methodologies to extract meaningful information
- Cyber: central information hub, which aggregates all the information from various sources
- Cognition: presentation of the monitored system to transfer knowledge to the users
- Configuration: application of decisions, made at the cognition level, in the physical world
These measures produce a system in which machines can react themselves from perturbations by collaboratively finding alternative solutions and preventing operations failures
Evolution of the decision-making process in production management
CPPS change the decision-making process by which activities are planned and executed in manufacturing systems. Fig. 2 shows, the traditional hierarchical structure of Computer-Integrated Manufacturing (CIM) systems, could be replaced with a scheme, that can be imagined as a set of intelligent entities working together and acting control on the physical resources to achieve the goals set by the highest strategic level of the company [4].
This architecture allows both vertical and horizontal integration of decisions, meaning planning activities and production operations will be increasingly intertwined, with CPPSs will be able to plan, execute and monitor the entire process, in a recursive and autonomous way. Human decision-makers will set the goals and guidelines for the firm and an ERP will get and translate them for the rest of the system, in particular to the CPPS that handles the production system.
Even if centralized coordination is still present, in a CPPS, the intelligence of decision-making power is widely distributed within the whole system. This means no one entity has the complete information needed to make a decision, which must therefore arise from their interaction, thanks to locally available information and a collaboration protocol [5].
Open challenges
Although there have been made great progresses on both CPS conceptualization and application, it is still in an embryonic stage, and a not exhaustive list of the main challenges includes:
-
Data management: storage and analysis of large heterogeneous data from different connected devices with different communication protocols, showing real-time results; significant issues about data privacy and security are raised.
-
Systems integrability: integrate all the subsystems into one, allowing communication using mutual platforms; systems reliability and safety are fundamental requirements.
-
Systems performance: optimal trade-off between entities' competition and cooperation; global optimization and local autonomy; predictability and disturbances reactivity.
The main challenge of the next few years is to provide proof of concepts, industrial applications, and laboratory developments able to prove, the integration of CPSs in the current industrial practices will transform today's factories into an Industry 4.0 factories, with significant advantages in terms of productivity, flexibility, and cost reduction.
CPS in operational planning by PlaniSense
The connection between physical assets and computational tools we emphasized, introduced new possibilities to schedule, measure, and control production activities. Particularly, scheduling processes have been pointed out as the main challenges in designing and exploiting CPPS [6].
Based on our experience 3 main factors strengthen this claim and guide our efforts to develop solutions that capture recent innovations to meet the needs of planners:
- Incorporate scheduling activities into the broader development of a production plan, with the ultimate aim of optimizing certain performance criteria.
- Deal with the many unforeseen events that can occur at operational level (changes in demand, absenteeism, shortages, machine breakdowns, delays, etc.).
- Enable collaborative, decentralized decision-making to effectively orchestrate increasingly complex and distributed production systems.
BIBLIOGRAPHY
[1] M. N. O. Sadiku, Y. Wang, S. Cui, and S. M. Musa, ‘Cyber-Physical Systems: A Literature Review’, Eur. Sci. J. ESJ, vol. 13, no. 36, p. 52, Dec. 2017.
[2] O. Cardin, ‘Classification of cyber-physical production systems applications: Proposition of an analysis framework’, Comput. Ind., vol. 104, pp. 11–21, Jan. 2019.
[3] J. Lee, B. Bagheri, and H.-A. Kao, ‘A Cyber-Physical Systems architecture for Industry 4.0-based manufacturing systems’, Manuf. Lett., vol. 3, pp. 18–23, Jan. 2015.
[4] L. Monostori et al., ‘Cyber-physical systems in manufacturing’, CIRP Ann., vol. 65, no. 2, pp. 621–641, 2016.
[5] J. C. Bendul and H. Blunck, ‘The design space of production planning and control for industry 4.0’, Comput. Ind., vol. 105, pp. 260–272, Feb. 2019.
[6] L. Monostori, ‘Cyber-physical Production Systems: Roots, Expectations and R&D Challenges’, Procedia CIRP, vol. 17, pp. 9–13, 2014.