Les systèmes de production cyber-physiques
Sep 18, 2023 1:50:34 PM - 9 min read
Nicola La Palombara
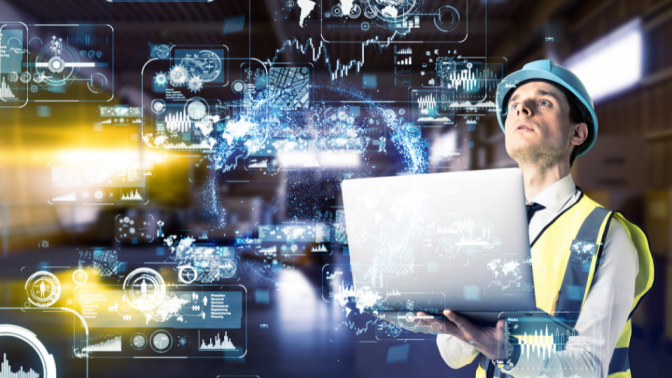
Poussée par les exigences de produits hautement personnalisés, la complexité croissante des systèmes de production ou encore le raccourcissement des cycles de vie des produits, la quatrième révolution industrielle fait référence à l’adoption de technologies innovantes pour stimuler la numérisation et l’intégration des activités de la chaîne de valeur.
L’un des principaux défis de l’Industrie 4.0 est l’introduction d’architectures décentralisées. Ces dernières permettent la collaboration entre des entités autonomes afin d’obtenir des performances de production plus élevées. Ces dernières permettent la collaboration entre des entités autonomes afin d’obtenir des performances de production plus élevées.
Dans cet article, nous analyserons les principes de ce nouveau paradigme et ses impacts potentiels sur la planification opérationnelle.
Les systèmes cyber-physiques, point de rencontre entre le monde virtuel et le monde physique
Le nouveau paradigme, qui englobe toutes les caractéristiques de l’Industrie 4.0, est connu sous le nom de système cyber-physique (CPS) et repose sur l’idée d’impliquer des objets intelligents (des agents) tels que des machines, des pièces et des produits afin d’obtenir des données en temps réel (contrôle), de les évaluer (calcul) et de communiquer les résultats (communication)[1]. Les CPS représentent une combinaison de composants physiques (capteurs et actionneurs) et cybernétiques (systèmes informatiques) avec une connexion réseau constante, un contrôle autonome et un comportement qui s’adapte à l’évolution de l’environnement. Les CPS extraient de grandes quantités de données des processus physiques et créent une copie virtuelle du monde physique, communément appelée jumeau numérique.
La représentation numérique permet de cartographier de manière dynamique et réaliste les ressources et les activités physiques dans l’espace virtuel pour le traitement ultérieur des données, la simulation et l’interconnexion des machines afin de pouvoir prendre des décisions décentralisées basées sur les conditions du système en temps réel.
De cette manière, les CPS présentent une approche efficace pour développer et conduire une stratégie de planification optimale basée sur les résultats des simulations de jumeaux numériques.
Systèmes cyber-physiques dans les systèmes de planification et de contrôle de la production
Parmi les nombreuses utilisations possibles, l’application des CPS dans le domaine de la gestion de la production a donné naissance au terme de systèmes de production cyber-physiques (CPPS). Nous pouvons définir les CPPS comme des systèmes de systèmes dotés d’une certaine autonomie, qui coopèrent pour prendre des décisions à tous les niveaux des activités de production, ce qui leur permet de réagir à des événements imprévus et d’évoluer dans le temps. Ces systèmes utilisent des interfaces de communication à la fois pour exploiter la coopération des CPS entre eux et pour permettre une collaboration approfondie avec les humains, l’objectif final étant de parvenir à des systèmes intelligents, résilients et auto-adaptatifs [2].
La Fig. 1 propose une synthèse intégrée de ces caractérisations, en soulignant que l’intelligence, la connectivité et la réactivité sont les trois principales caractéristiques des CPS.
Les capacités clés mises en avant par cette architecture sont les suivantes:
- Autodétection : les CPS capturent, exploitent et partagent en permanence des informations en provenance et à destination de l’environnement.
- Autodétermination : les CPS peuvent prendre des décisions fondées sur des données en fonction de l’état du système capté en temps réel.
- Autoadaptation : les CPS sont réactifs face à des événements inattendus grâce à une transmission plus rapide de l’information dans l’ensemble du système.
Attentes vs mise en œuvre
L’architecture 5C [3] détaille la mise en œuvre étape par étape des CPS pour les applications de production :
- Connexion intelligente : intégration de tous les éléments dans l’espace physique pour collecter des données.
- Conversion des données : outils et méthodologies permettant d’extraire des informations significatives.
- Cyber : centre d’information central qui regroupe toutes les informations provenant de diverses sources.
- Cognition : présentation du système surveillé pour transférer les connaissances aux utilisateurs.
- Configuration : application des décisions prises au niveau cognitif dans le monde physique.
Ces mesures produisent un système dans lequel les machines peuvent réagir aux perturbations en trouvant de manière collaborative des solutions alternatives au plan initial.
Évolution du processus décisionnel dans la gestion de la production
Le CPPS modifie le processus décisionnel par lequel les activités sont planifiées et exécutées. La Fig. 2 montre comment la structure hiérarchique traditionnelle des systèmes de fabrication intégrés (CIM) peut être remplacée par un ensemble d’entités intelligentes travaillant ensemble et contrôlant les ressources physiques pour atteindre les objectifs fixés par le niveau stratégique le plus élevé de l’entreprise [4].
Cette architecture permet une intégration à la fois verticale et horizontale des décisions, ce qui signifie que les activités de planification et les opérations de production seront de plus en plus imbriquées, les CPPS étant capables de planifier, d’exécuter et de contrôler l’ensemble du processus, de manière récursive et autonome. Les décideurs humains fixent les objectifs et les règles de gestion à respecter.
Même si la coordination centralisée est toujours présente, le pouvoir de décision est largement réparti dans l’ensemble du système. Cela signifie qu’aucune entité ne dispose de l’ensemble des informations nécessaires à la prise de décision, qui doit donc résulter de leur interaction, grâce à des informations disponibles localement et à un protocole de collaboration [5].
Défis ouverts
Bien que la conceptualisation et l’application des CPS aient fait de grands progrès, elles en sont encore à un stade embryonnaire, et une liste non exhaustive des principaux défis comprend
- Gestion des données : stockage et analyse d’un grand nombre de données hétérogènes provenant de différents dispositifs connectés avec différents protocoles de communication et présentation de résultats en temps réel ; des questions importantes concernant la confidentialité et la sécurité des données sont soulevées.
- L’intégrabilité des systèmes : intégrer tous les sous-systèmes en un seul, permettant la communication à l’aide de plateformes mutuelles ; la fiabilité et la sécurité des systèmes sont des exigences fondamentales.
- Performance des systèmes : compromis optimal entre la concurrence et la coopération des entités ; optimisation globale et autonomie locale ; prévisibilité et réactivité aux perturbations.
Le principal défi des prochaines années est de fournir des preuves de concept, des applications industrielles et des développements en laboratoire capables de prouver que l’intégration des CPS dans les pratiques industrielles actuelles transformera les usines avec des avantages significatifs en termes de productivité, de flexibilité et de réduction des coûts
Les CPS dans la planification opérationnelle par PlaniSense
La connexion entre les actifs physiques et les outils informatiques que nous avons soulignée a introduit de nouvelles possibilités pour planifier, mesurer et contrôler les activités de production. En particulier, les processus d’ordonnancement ont été désignés comme les principaux défis à relever dans la conception et l’exploitation des systèmes de planification de la production [6].
Sur la base de notre expérience, trois facteurs principaux renforcent cette affirmation et guident nos efforts pour développer des solutions qui intègrent les innovations récentes afin de répondre aux besoins des planificateurs :
- Incorporer les activités d’ordonnancement dans l’élaboration plus large d’un plan de production avec l’objectif final d’optimiser certains critères de performance.
- Faire face aux nombreux événements imprévus qui peuvent survenir au niveau opérationnel (changements dans la demande, absentéisme, pénuries, pannes de machines, retards, etc.).
- Permettre une prise de décision collaborative et décentralisée pour orchestrer efficacement des systèmes de production de plus en plus complexes et distribués
BIBLIOGRAPHIE
[1] M. N. O. Sadiku, Y. Wang, S. Cui et S. M. Musa, 'Cyber-Physical Systems : A Literature Review", Eur. Sci. J. ESJ, vol. 13, no. 36, p. 52, déc. 2017.
[2] O. Cardin, " Classification des applications des systèmes cyber-physiques de production : Proposition d'un cadre d'analyse', Comput. Ind., vol. 104, p. 11-21, janv. 2019.
[3] J. Lee, B. Bagheri et H.-A. Kao, 'A Cyber-Physical production systems : A Cyber-Physical production systems. Kao, 'A Cyber-Physical Systems architecture for Industry 4.0-based manufacturing systems', Manuf. Lett, vol. 3, pp. 18-23, janv. 2015.
[4] L. Monostori et al, "Cyber-physical systems in manufacturing", CIRP Ann, vol. 65, no. 2, pp. 621-641, 2016.
[5] J. C. Bendul et H. Blunck, " The design space of production planning and control for industry 4.0 ", Comput. Ind., vol. 105, pp. 260-272, fév. 2019.
[6] L. Monostori, 'Cyber-physical Production Systems : Roots, Expectations and R&D Challenges', Procedia CIRP, vol. 17, pp. 9-13, 2014.