The five fundamental steps of supply chain management include planning, sourcing, production, delivery, and return. Each step requires meticulous coordination and collaboration to maximize efficiency and profitability.
What is Supply Chain Management?
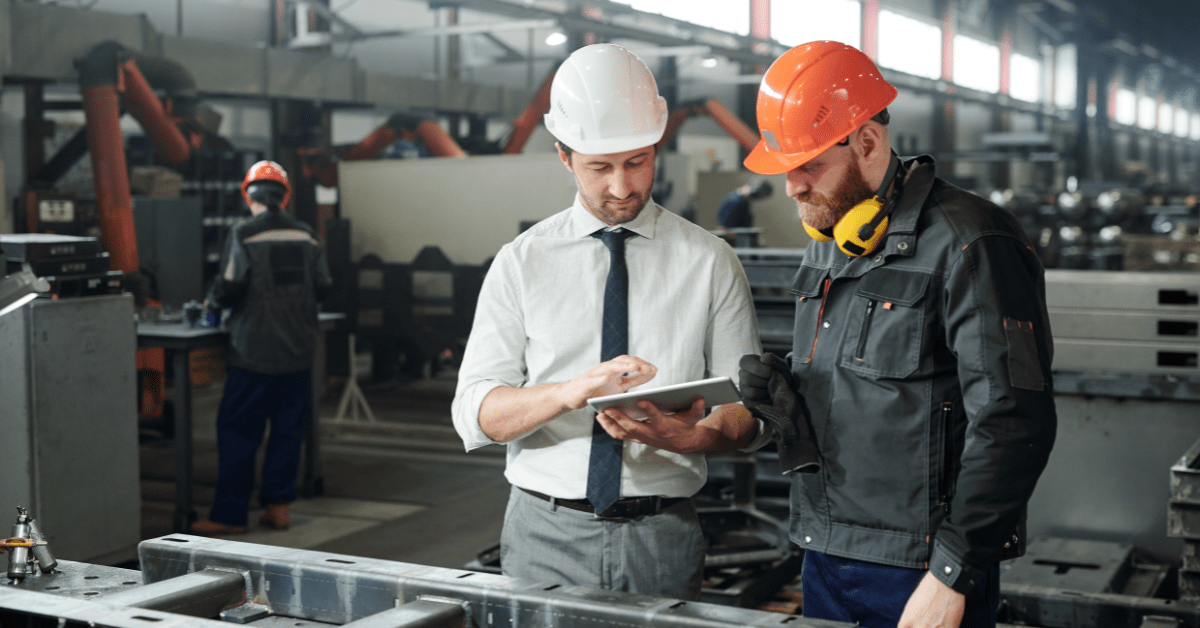
Supply Chain Management is a crucial field that encompasses all the processes involved in the production and distribution of goods and services. This starts at the resource planning stage and extends through the sourcing of raw materials, through production, to the delivery of the final product to the consumer. An efficient supply chain is vital to maintain competitiveness and respond quickly to changing market demands.
In the modern way businesses operate, the ability to maintain smooth production, while minimizing costs and maximizing customer satisfaction, is critical. Appropriate procurement and purchasing strategies, an optimized production process and well-coordinated logistics distribution all contribute to successful supply chain management. In addition, the adoption of appropriate information technology facilitates the integration and synchronization of the different parts of the chain.
Sustainability and social responsibility have become an essential part of supply chain management. Companies are increasingly expected to be able to adopt environmentally friendly and ethically responsible practices throughout their value chain. This includes not only environmental efficiency, but also social equity, two essential components for building a strong and sustainable reputation.
Key Points
- Supply chain efficiency is central to business competitiveness.
- Technology and process coordination are key to chain optimization.
- Sustainability and social responsibility have become key criteria in supply chain management.
Fundamentals of Supply Chain Management
Effective supply chain management is based on several fundamental principles, which are essential to optimize operations and ensure responsiveness to market demands.
- Strategic alignment: The supply chain should be in alignment with the company's strategic goals. This includes understanding customer expectations and adapting operations to meet them effectively.
- Supplier Onboarding
- Synchronization with sales targets
- Agility: Businesses need to be able to react quickly to market changes and unforeseen demands.
- Process Flexibility
- Adaptability
- Cost optimization: Controlling costs at every stage of the supply chain is crucial for competitiveness.
- Reduction of unnecessary expenses
- Profitability analysis
- Continuous Improvement: It is important to embed a culture of continuous improvement to optimize processes and identify opportunities for cost reduction and quality improvement.
- Use of feedback
- Implementation of methodologies such as Lean management
- Risk Management: Identifying, assessing, and mitigating risks to ensure business continuity is a key component of supply chain management.
- Business Continuity Plans
- Supplier Diversification Strategies
- Collaboration: Collaboration between all actors in the supply chain leads to improved efficiency and responsiveness
- Information Sharing
- Strategic Partnerships
Adherence to these principles is fundamental to a robust and responsive supply chain that can support the company's long-term goals while providing added value to the end customer.
Enterprise Resource Planning
Enterprise Resource Planning plays a crucial role in aligning material and human resources with a company's operational strategy, ensuring the efficiency and optimization of production and distribution
Demand Forecasting
Demand forecasting is essential for enterprise resource planning. It involves the use of statistical tools and predictive models to assess future needs for products and services. Companies leverage historical data and market trends to prepare accurate estimates, allowing them to respond effectively to changing demand.
- Historical Data: Using sales history to anticipate future needs.
- Trend Analysis: Observing changes in consumer behavior and adapting accordingly.
- Predictive Models: Application of quantitative methods to estimate future demand.
Production Resource Planning
Production resource planning refers to the allocation and organization of resources needed to complete the production schedule. It ensures the availability of raw materials, personnel and equipment in order to meet the expected demand in an efficient manner.
- Resource Allocation: Allocation of raw materials, machinery, and labor where they are needed.
- Capacity Planning: Matching production capacity to forecasted demand.
- Scheduling: Sequencing and timing of production activities to maximize yield.
These elements of planning are interdependent; Inaccurate demand forecasting can lead to inefficient production resource planning, and vice versa.
Procurement & Purchasing
Procurement and purchasing are essential components of the supply chain, involving the acquisition of goods and services necessary to conduct a company's business. Effectively managing these processes can lead to reduced costs and improved quality and efficiency.
Supplier Relationship Management
Strategic supplier relationship management involves the evaluation and selection of suppliers, as well as the development of long-term partnerships. Companies should establish clear criteria for suppliers, which can include delivery performance, product quality, cost, and the company's ability to innovate. The following table summarizes the selection criteria:
Selection Criteria |
Description |
Delivery Performance |
Compliance with delivery deadlines and conditions. |
Product Quality |
Compliance with quality standards and expectations. |
Cost |
Price competitiveness and overall tariff structure. |
Capacity for innovation |
Ability to make continuous improvements. |
These criteria not only ensure that suppliers can meet the current needs of the business, but also that they are able to adapt to future requirements.
Purchasing Strategies
The development of effective purchasing strategies must take into account the company's cost, quality and time objectives. A purchasing strategy can take several forms depending on the company's situation, such as group purchasing, negotiating long-term contracts, or outsourcing. The methods adopted are aimed at leveraging buyer power, minimizing risk, and optimizing inventory management. Here is a summary of the main strategies:
- Group Purchasing : Achieve economies of scale by aggregating purchasing volumes.
- Long-Term Contracts : Securing prices and guaranteeing the availability of goods or services over an extended period of time.
- Outsourcing : Outsourcing certain activities or services to third parties to focus on the core business.
Each procurement strategy should be evaluated based on the specific objectives of the company and the market environment in which it operates.
Production Operations
Production operations within supply chain management are crucial to ensure efficiency and value for money. They involve rigorous inventory management and precise production logistics to meet market demands.
Inventory Management
Inventory management is the process of maintaining the optimal level of stock to avoid stock-outs or surpluses. Sales forecast analysis and inventory turnover are two key components. It is essential to adopt inventory management tools that allow you to track stock levels, current orders, and necessary replenishment in real time.
- Real-time tracking: It ensures an accurate view of the available stock.
- Sales forecasts: These guide the quantities to be kept in reserve.
- Inventory turnover: Key indicator to avoid obsolescence.
Production Logistics
Production logistics is concerned with the organization, planning and supervision of production flows. It aims to optimize manufacturing processes for better resource allocation and reduced production costs.
- Production Planning:
- Definition of quantities to be produced
- Selection of the necessary resources
- Management of material flows:
- Conveyance of raw materials
- Internal transport of semi-finished products
Distribution & Logistics
Distribution and logistics are crucial to the success of the supply chain, ensuring that products arrive at the right place, at the right time and in optimal conditions.
Transportation Management
Transportation management is responsible for planning, executing, and optimizing the movement of goods. It involves:
- The selection of modes of transport (road, rail, marine, air) according to their efficiency and cost.
- Negotiating contracts with carriers to ensure competitive rates.
- The use of transportation management systems (TMS) to track shipments in real-time.
Warehousing & Handling
Warehousing and handling refers to the preservation and handling of products in warehouses.
Key Elements:
- Optimisation of storage space through strategic arrangement of goods.
- Inventory management for efficient product turnover.
- The application of safety standards to protect both personnel and goods.
Customer Relationship Management
Success in Supply Chain Management involves meeting customer requirements, both in terms of customer service and order fulfillment. Both of these aspects are essential for maintaining a long-lasting and profitable customer relationship.
Client service
Customer service in supply chain management is the first point of contact with customers. They must be efficient and able to respond quickly to customer requests and issues. Customer service agents need to have a 360-degree view of customer information in order to offer personalized, high-quality support. Here are some key elements to optimize:
- Availability: Extended business hours for customer support.
- Multichannel: Offering support through various channels such as phone, email, live chat, and social media.
- Training: Agents trained to provide accurate information about products, services, and order tracking.
- Tools: Customer relationship management (CRM) systems to keep track of all customer interactions and preferences.
Order Fulfillment
Order fulfillment is a crucial element that reflects the operational efficiency of the supply chain and directly influences customer satisfaction. It consists of several components:
- Order accuracy: Ensuring that the right product is delivered to the right customer.
- Speed of delivery: Minimization of the time between receipt of the order and delivery.
- Returns Management: Efficient process for handling returns or exchanges.
An optimized supply chain must ensure accurate inventory management and order fulfillment systems that allow for a real-time overview to anticipate and respond to customer demands.
Supply Chain Information Technology
Information technology plays a crucial role in enabling visibility, efficiency, and speed in supply chain management. They are essential for synchronizing and optimizing the flow of products, information, and finances.
Management Information Systems
Management Information Systems (MIS) include tools such as Enterprise Resource Planning (ERP) and Warehouse Management Systems (WMS). They make it possible to centralize and process operational data to improve decision-making. For example, an ERP integrates various business functions, such as purchasing, production, sales, and distribution.
- ERP (Enterprise Resource Planning)
- Integration of business functions
- Value for money
- Improved planning
- WMS (Warehouse Management Systems)
- Optimization of warehouse operations
- Real-time inventory management
- Speeding up picking and shipping processes
Data Integration
Data integration refers to the process of unifying information from different sources, with a view to obtaining a consistent and holistic view of operations. This is often achieved through EDI (Electronic Data Interchange) and APIs (Application Programming Interfaces).
- EDI (Échange de Données Informatisé)
- Automation of the exchange of business documents
- Reduction of manual entry errors
- Improved Operational Efficiency
- API (Interfaces de Programmation d'Applications)
- Connectivity between different IT systems
- Enables real-time communication
- Facilitates innovation and integration of new features
Sustainability and Social Responsibility in the Supply Chain
Supply chain sustainability highlights the importance of creating distribution networks that respect the environment and reduce waste at all levels. In this way, companies are striving to minimize their carbon footprint and promote the circular economy.
When it comes to social responsibility, organizations focus on the impact their supply chain can have on communities. They are committed to respecting human rights, ensuring fair working conditions and fighting corruption.
Key Factors |
Descriptions |
Ecological |
Reduce CO2 emissions, optimize the use of resources. |
Economic |
Ensure effective management for sustainable sourcing. |
Social |
Ensure the well-being of workers and respect for local communities. |
Certifications, such as ISO 14001 and SA8000, play a key role in attesting to compliance with environmental and social standards. Regular audits ensure continued adherence to these standards.
Collaboration with suppliers is key to establishing sustainable practices. It often involves sharing knowledge and resources to help suppliers achieve shared sustainability goals.
Transparency is also crucial. Sustainability reports and key performance indicators (KPIs) give stakeholders information on progress.
In summary, integrating sustainability and social responsibility into supply chain management has become imperative for modern companies concerned about their impact on society and the planet.
FAQ
The role of supply chain management in a company is to oversee and coordinate all activities related to the flow of goods and services, from the acquisition of raw materials to the delivery of final products to consumers, while optimizing costs and improving customer satisfaction.
The main principles that govern supply chain management include transparency, flexibility, responsiveness, efficiency and collaboration between all links in the chain, aiming to reduce waste and increase value for the consumer.
Supply chain management can be defined as the set of processes and methods used to effectively coordinate and organize the movement of goods, services, and information from supplier to customer.