An ERP (Enterprise Resource Planning) for the supply chain offers several benefits. It helps integrate and centralize critical logistics processes, improve planning and forecasting, reduce costs, optimize resource utilization, and improve collaboration between different stakeholders.
Strategic Supply Chain Management: The Essential Role of ERP
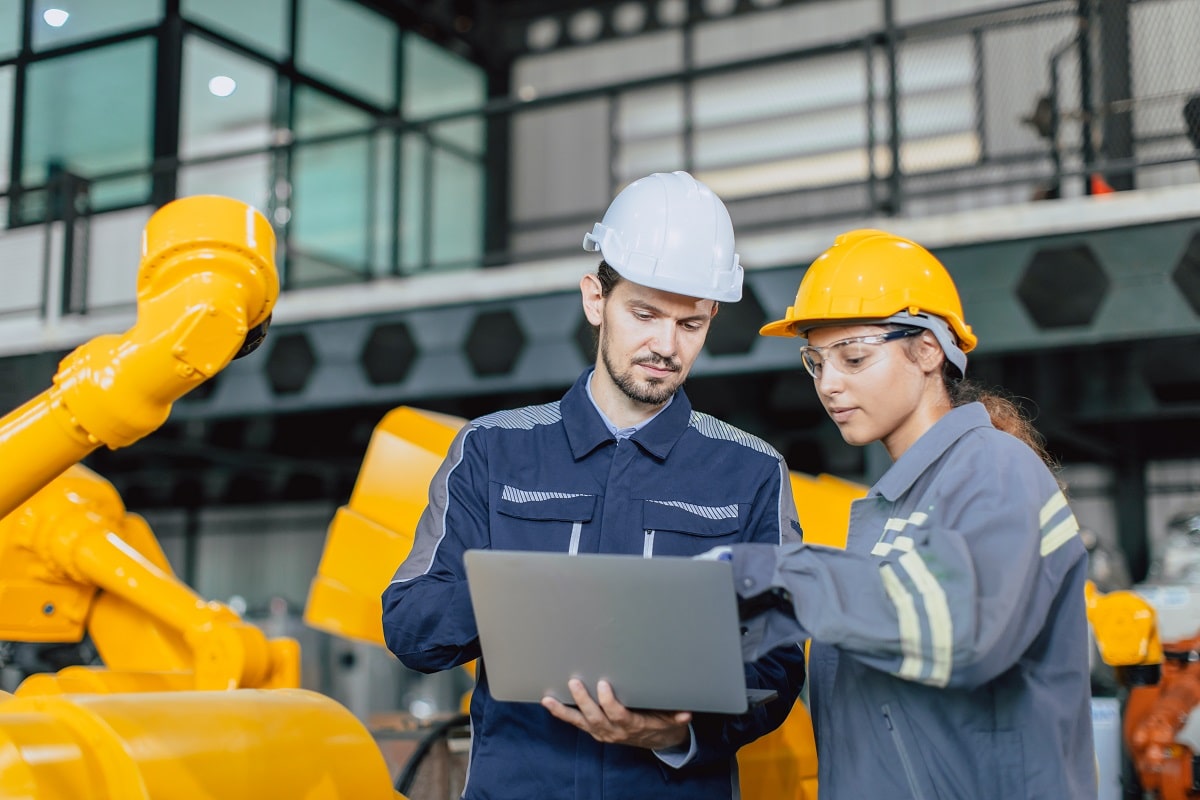
Enterprise Resource Planning (ERP) in the supply chain plays a crucial role in ensuring the efficiency and profitability of modern businesses. At the heart of this strategy are integrated IT systems that help manage and optimize all stages of the procurement process, from production to sales, sales and customer service.
The fundamental concepts of ERP encompass the centralization of data, the automation of processes, and the real-time management of all company resources. With these tools, companies can improve their competitiveness in the market, anticipate and respond quickly to fluctuations in demand, while reducing supply chain costs and time.
Key Points
- ERP helps optimize the supply chain through data centralization and process automation
- Businesses can improve competitiveness and reduce costs with real-time ERP management
- ERP tools help to anticipate and respond quickly to fluctuations in market demand
ERP Fundamentals
The concept of Enterprise Resource Planning (ERP) was initiated in the 90s and has revolutionized the approach to business management. The goal of ERP is to centralize all operational and financial information in a single system, providing a holistic view of the business.
- Resource Planning: ERP helps manage the availability and distribution of company resources, such as employees, equipment, and inventory. It optimizes resource allocation based on internal and external needs and constraints.
- Process management: The system integrates key business processes, such as production, logistics, procurement, and customer management. It facilitates communication between departments and allows all processes to be monitored and optimized.
- Data Integration: ERP centralizes data from different departments and applications, making it easy to share and improve decision-making.
Benefits |
Disadvantages |
Centralization of data |
High cost of implementation |
Process Optimization |
System Rigidity |
Improved communication |
Employee Adoption |
There are several ERP solutions available on the market, including solutions tailored to SMBs and large enterprises, as well as industry-specific solutions. Some ERPs are installed locally in the company, while others are available in cloud mode.
An ERP implementation project typically includes the following steps:
- Needs analysis and specifications
- Vendor and Solution Selection
- Customization of the solution
- Employee set-up and training
- Maintenance and evolution of the system
In summary, the concept of ERP is a valuable tool for a company looking to optimize its processes and resource management. Thanks to the centralization and integration of data, the ERP facilitates decision-making and improves communication between departments. However, it is essential to think carefully about the adoption of an ERP solution by considering the issues and challenges related to its implementation and evolution.
Benefits and Challenges of ERP in the Supply Chain
Improved Efficiency
One of the main benefits of an ERP system in the supply chain is improved efficiency. A well-designed ERP can:
- Automate repetitive and time-consuming tasks, freeing up time to focus on higher value-added activities.
- Standardize data across different departments and supply chain partners, allowing for better decision-making and smoother coordination.
- Optimize resource allocation and capacity planning, with better visibility into inventory levels and demand forecasts.
In addition, an ERP can help reduce costs by minimizing excess inventory, avoiding material shortages, and improving customer service levels.
Risk Management
ERP also plays an important role in managing risk within the supply chain. For example, it can:
- Monitor supplier performance in real time and identify potential quality or delivery time issues, allowing you to anticipate and limit negative consequences.
- Evaluate different scenarios and their impact on the supply chain, considering factors such as changes in demand, fluctuations in raw material costs, or logistical disruptions.
- Ensure full traceability of products and batches, from the supplier to the end customer, which facilitates the management of possible recalls and helps to strengthen customer trust in the brand.
Nevertheless, implementing an ERP in the supply chain is not without its challenges. Some of the main obstacles include:
- High cost: The investments required to acquire, deploy, and maintain an ERP system can be considerable, especially for small and medium-sized businesses.
- Complexity: ERP systems are often complex and require extensive user training, who must adapt to new processes and work tools.
- Integration: The success of an ERP implementation depends largely on the quality of the integration with other existing systems within the company and its partners.
Despite these challenges, it is indisputable that the potential benefits of ERP in the supply chain seriously justify its adoption and adaptation to the specific needs of each organization.
Optimization of ERP processes in the supply chain
Optimizing ERP processes in the supply chain is essential to ensure proper organization and better management of product flows and costs. This section will focus on two key subsections for optimizing ERP processes: demand forecasting and production planning.
Demand Forecasting
Demand forecasting is crucial for reducing costs and improving supply chain efficiency. It allows businesses to better anticipate future resource needs and plan accordingly. Key considerations for demand forecasting include:
- Sales history: Past sales data is essential for predicting future trends.
- Market trends: Forecasters need to monitor market trends to anticipate fluctuations in demand.
- Seasonality: The demand for some products can vary depending on the seasons. It is important to consider this when forecasting.
Modern ERP systems will incorporate advanced forecasting tools, such as machine learning and artificial intelligence, to improve the accuracy of their predictions.
Production planning
Production planning is a key step in synchronizing supply and demand in the supply chain. ERPs make this task easier by offering tools to optimize production capacity, inventory management, and purchasing organization. Here are some key things to consider when planning production:
- Optimizing Production Capacity: It is important to ensure that factories are operating at their optimal level. This is achieved by harmonizing available resources and raw material requirements.
- Calculation of net requirements: It is essential to determine the necessary quantities of each raw material based on the expected demand.
- Capacity planning: ERPs allow for better management of human and material resources to optimize production.
- Inventory management: Effective inventory management helps reduce costs and prevent stock-outs.
- Reorder Point Method: This method is used to determine the optimal amount of inventory to maintain based on expected demand.
- Just-in-time replenishment: ERP systems help plan inventory replenishment in a way that minimizes storage costs while still meeting demand.
- Procurement organization: Negotiating purchase contracts and managing relationships with suppliers is facilitated by ERP systems. They offer tools to evaluate supplier performance, track orders, and manage delivery times.
The optimization of ERP processes in the supply chain, through better demand forecasting and more efficient production planning, allows for improved cost, inventory and lead time management, thus ensuring a better overall performance for the company.
ERP Use Cases in the Supply Chain
The use of an ERP (Enterprise Resource Planning) system in supply chain management helps improve the performance and efficiency of a company. Here are some use cases where ERP helps optimize processes within the supply chain.
- Demand Planning & Forecasting: ERP allows you to forecast demand based on historical data and market trends. It facilitates the implementation of short- and long-term production plans by considering production capacity, human resources, and delivery times.
- Inventory management: The ERP system offers tools for precise inventory control, allowing for optimized inventory management. It helps determine ideal inventory levels, identify obsolete products, and reduce out-of-stock situations.
- Procurement Management: ERP helps companies streamline their purchasing processes by automating the management of purchase requisitions, quotes, and orders. It also helps track and control supplier performance, assess risk, and negotiate the best possible contracts.
- Production Planning: ERP can make it easier to create production plans by considering capacity constraints, labor costs, and materials. It helps to create production orders, plan preventive maintenance of machines, and optimize production times.
Here's an example of a table showing the benefits of using an ERP system in the supply chain:
Function |
Benefits |
Demand Planning & Forecasting |
Better demand predictions, demand-adjusted production plans |
Inventory Management |
Optimized inventory levels, reduction of obsolete products and stock-outs |
Procurement Management |
Automated purchasing processes, better negotiations with suppliers |
Production planning |
Optimization of production times, reduction of unplanned maintenance |
ERP helps improve supply chain management by offering tools for functions such as demand forecasting, inventory management, purchasing management, and production planning. The adoption of these solutions can lead to significant gains in performance, efficiency, and profitability for businesses.
Frequently asked questions
To implement an ERP to optimize the supply chain, it is important to follow a few key steps:
1) define the company's specific goals and needs,
2) choose an ERP adapted to these needs,
3) set up a dedicated project team,
4) train users on the system, and
5) plan and manage the implementation and maintenance phases.
The main modules of a supply chain ERP typically include purchasing management, inventory management, material requirements planning (MRP), warehouse management, production management, shipping and logistics management, returns management, and quality management.
Yes, there are specialized supply chain management ERPs that mainly focus on logistics features and processes. These ERPs are designed to meet the specific needs of companies operating in the logistics and supply chain.
The estimated cost for implementing an ERP system in the supply chain varies depending on several factors such as the size of the company, the complexity of the processes, the number of users, the customization required, and the duration of the project. This makes it difficult to provide an accurate figure without knowing the specific details of the project.
Key success factors in choosing an ERP for the supply chain include understanding the specific needs of the business, selecting an experienced ERP vendor, training users, planning and effective project management, and building strong partnerships with internal and external stakeholders.