Operational planning: reconciling consistency and responsiveness
Nov 2, 2023 10:40:42 AM - 8 min read
.png)
PlaniSense
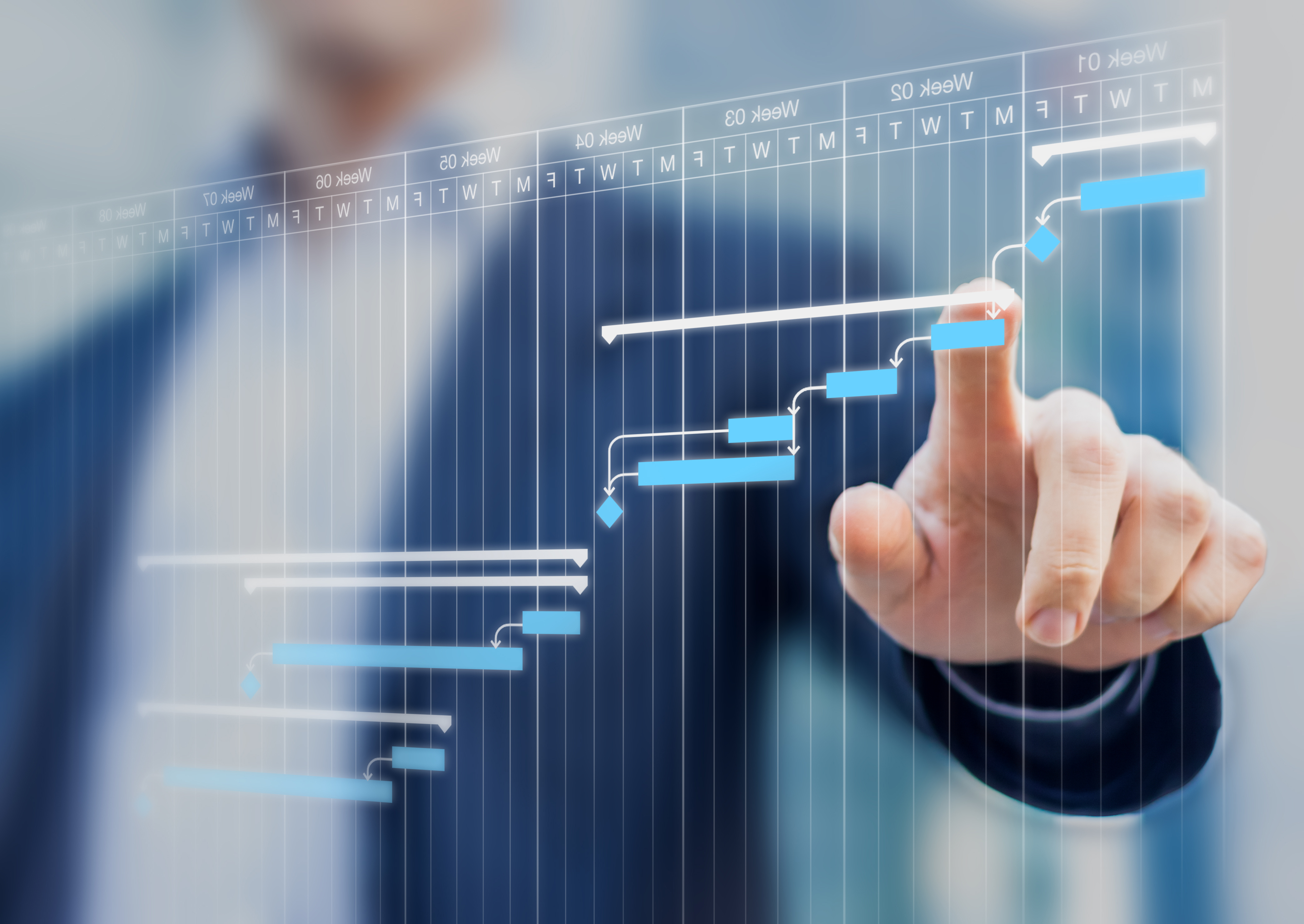
Introduction
Operational planning needs consistency to be effective. The stabilization of plans has long been the means of guaranteeing coherence between the different levels of hierarchical planning. In today's world, which some describe as a VUCA (Variability, Uncertainty, Complexity, Ambiguity) world, maintaining consistency by stabilizing plans alone runs counter to the need for reactivity that is essential to all companies.
In this article, we explore ways of combining consistency and responsiveness, using the right planning methods and tools.
Operational planning, a central process in supply chain management
Operational planning involves projecting activity into the future and anticipating resource requirements. This process is not static but gives rise to a series of cyclical adjustments designed to adapt plans to observed or expected internal changes, such as the availability of production resources, and external changes, such as variations in demand or the availability of components.
Operational planning is a cross-functional process, insofar as it concerns procurement, production and distribution. Operational planning is horizontally integrated into the basic functions of the supply chain.
Furthermore, operational planning is part of an overall hierarchical process, from Sales and Operation Planning (S&OP) through Master Production Planning and Net Requirements Planning to scheduling. Operational planning is vertically integrated into the overall hierarchical planning process.
The figure below illustrates the dual horizontal and vertical integration of operational planning.
Coherence: a prerequisite at the heart of planning challenges
Coherence in operational planning is as much a question of horizontal consistency as of vertical consistency.
Vertical coherence poses a major challenge. Indeed, strategic, tactical and operational planning are not homogeneous in terms of the variables they bring into play (horizon, time frame, level of aggregation, capability constraints) and the questions they seek to answer.
Because of these differences, the constraints of operational planning cannot reasonably be accommodated at the level of strategic and tactical planning. In other words, perfect harmony between the global and detailed levels is difficult to achieve.
The presence of constraints and business rules specific to each perimeter of the supply chain is another obstacle which, this time, stands in the way of coherent planning in its horizontal dimension.
Reconciling consistency and responsiveness in operational planning
Material Requirement Planning (MRP) is the most widely used planning method in the industry, and its main concern is to maintain vertical and horizontal consistency, thanks in particular to its downstream extension (DRP).
MRP is based on a sliding planning logic: in other words, the plan defined at a given point in time is regularly reviewed to adapt it to new conditions, both internal and external to the company. This principle poses no particular problem in a stable context. However, when conditions vary significantly between two planning cycles, the discrepancies between plans give rise to the phenomenon of plan nervousness. This leads to undesirable effects such as stock-outs and/or overstocking, or late deliveries. Similarly, these mechanisms, which cause whiplash effects, have a lasting impact on the performance of upstream and downstream supply chains.
Stable planning ensures better adherence to plans at all levels of the supply chain, and consequently greater consistency. The frozen horizon concept is a well-known device for stabilizing production plans. However, forcing plan stability by freezing quantities over a given horizon is not a miracle solution. In fact, fixed planning is not compatible with highly variable demand. Even if the horizon is frozen for short periods, sales opportunities may be missed and/or overstocks created. Freezing a plan also means ignoring internal events, such as breakdowns or quality problems, which can call into question the very feasibility of the plan.
As planning seeks to project an activity into a context of perpetual change, a dose of reactivity is required, even though maintaining consistency remains essential.
Reinventing existing solutions to meet new industrial challenges
How do planning and scheduling solutions meet different ERP objectives?
The role of Enterprise Resource Planning (ERP) modules is central to ensuring the vertical and horizontal consistency mentioned above. These systems preserve the integrity of data and the uniformity of assumptions used for planning. Nevertheless, ERPs are very limited when it comes to carrying out simulations to measure the effects of a change made necessary by the emergence of a new situation, or to comparing alternative scenarios. ERPs are rigid tools that are not designed to meet the need for responsiveness.
Planning and scheduling solutions make it possible to test and compare several scenarios in order to guide decision-making in the short, medium and long term. These tools also help decision-makers to make informed choices by anticipating the consequences of different strategies, while taking into account variations in demand and capacity constraints.
In short, planning and scheduling solutions promote reactivity to compensate for the rigidity of ERP designed above all to guarantee consistency.
Excel, the wrong answer to the reactivity challenge
Excel is often used to compensate for the shortcomings of a rigid ERP or an inoperative APS solution. Even if the practice is widely used and may appear to be locally and occasionally satisfactory, it's important to bear in mind that Excel suffers from a number of weaknesses in terms of robustness, scalability, maintainability, flexibility and security.
In fact, despite the proliferation of Excel files, the ERP remains the guarantor of the overall consistency of the planning process. Desynchronization between ERP and Excel data is a regular occurrence, as communication between the central system and these tools is often poor. This situation threatens the consistency that is central to planning.
Is it still possible to reconcile consistency and responsiveness?
Existing ERP/APS solutions are rigid and/or outdated, resulting in a proliferation of Excel files that are difficult to maintain and jeopardize the coherence of the decision-making process, for the reasons outlined above.
Based on modern technologies, PlaniSense is an end-to-end planning solution offering an intuitive scenario-based planning approach. Planners can simulate, anticipate and measure the impact of their decisions simply and immediately. Innovative visualization and analysis functionalities enable rapid comparison of alternatives on an objective basis, promoting reactivity in the face of fluctuating conditions.
PlaniSense interfaces synchronously with the main ERP systems on the market, guaranteeing consistency in the decision-making process at all levels.
What makes planning and scheduling tools better than Excel?
Excel is a versatile spreadsheet program that makes it easy to create automated spreadsheets, schedules, graphs and databases. Its interface makes it easy to outline a project, making it a popular tool with many manufacturers when they're looking for a simple solution to more complex alternatives.
However, it should be noted that Excel was primarily designed to manage digital information and provide data processing functionality in a stable environment. Indeed, some adjustments can quickly turn into a headache. Here are a few examples of manipulations that are difficult to perform in Excel:
- Adding or deleting a machine or piece of equipment that modifies capacity
- Updating a product portfolio by adding or deleting an item
- Move, cancel or modify a production order
- Share and validate a planning scenario
- Synchronize production stages and update plans accordingly
So, is it still possible to reconcile stability and reactivity?
In conclusion, these demand management, planning and scheduling solutions integrate the best of both worlds: high-performance optimization and automation algorithms, characteristic of Advanced Planning Systems (APS), and an ergonomic, intuitive Excel-like interface, designed to meet the needs of manufacturers. By combining these two aspects, these solutions offer a complete and effective approach to reconciling stability and reactivity in the planning and scheduling of industrial operations.
Drawing on modern technologies, the PlaniSense solution offers a completely different, intuitive, scenario-based approach. It features a planning model capable of integrating constraints, business rules and system configuration, and on which scenarios can be built.
Scenarios model possible variations in system parameters and planning assumptions. In this way, we can imagine, anticipate and measure the impact of solutions to be applied to each change in context, immediately and very simply. Innovative visualization and analysis functions also enable alternatives to be quickly compared on an objective basis, thus promoting reactivity in the face of new situations. In short, you can quickly make the right decisions.
PlaniSense is a publisher of innovative, intelligent planning solutions that enable you to be more flexible and efficient in an increasingly complex environment.
If you want to better manage the complexities of operational planning, contact us to discover our demand management, supply chain planning and scheduling solutions that reinvent the planner's job.